Production and testing of ASME B16.5 F51 Flanges for our Italian client
Last month, our team at Haihao Group was tasked with manufacturing a series of ASME B16.5 flanges for a client based in Italy. The order included both weld neck (WN) flange and blind (BL) flanges, produced in duplex stainless steel A182 UNS S31803 (commonly known as F51).
Below, I’d like to share a brief overview of the production process, inspection steps, and quality documentation we provided to ensure the flanges fully met project specifications.
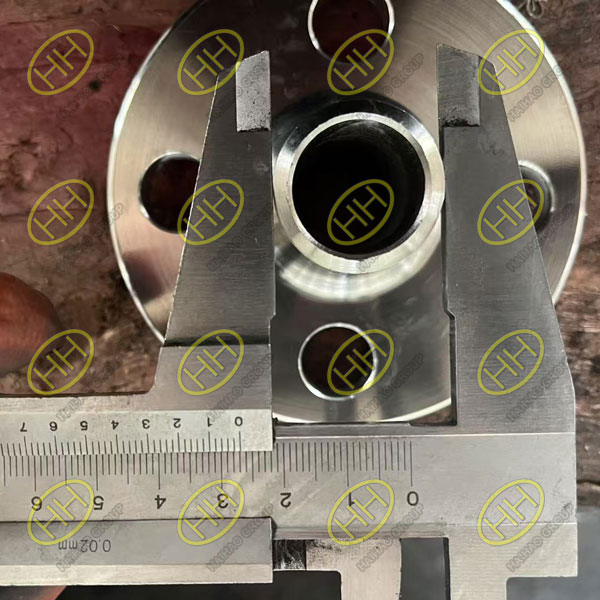
Inspection of ASME B16.5 A182 UNS S31803 weld neck flange for surface finish and dimensional tolerances
Product Scope and Specifications
The scope of supply comprised four main items:
-
6″ 150# Weld Neck RF Flanges (SCH10S)
-
6″ 150# Blind RF Flanges
-
3/4″ 150# Weld Neck RF Flanges (SCH40S)
-
3/4″ 150# Blind RF Flanges
All items were manufactured strictly to ASME B16.5 dimensional tolerances and supplied with raised face (RF) sealing surfaces.
The material—A182 UNS S31803 duplex stainless steel—was selected for its excellent combination of strength, toughness, and resistance to chloride stress corrosion cracking.
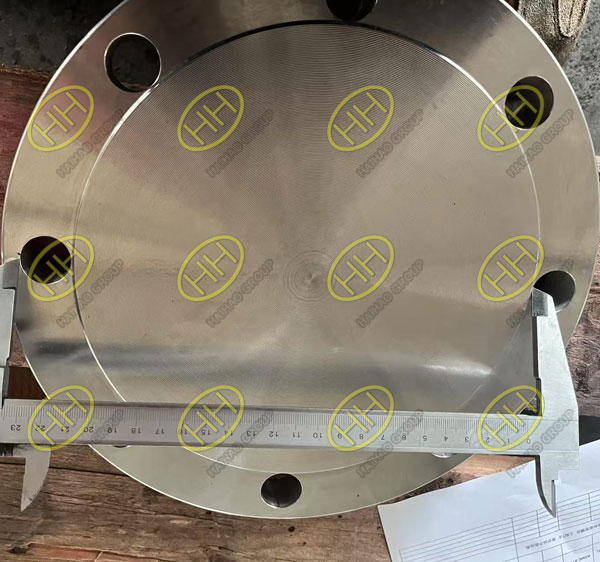
Inspection of ASME B16.5 A182 UNS S31803 blind flange for surface finish and dimensional tolerances
Raw Material Traceability and Documentation
One area many customers focus on is material traceability, especially for duplex stainless applications. For this project, we provided:
✅ Original mill certificates for raw forgings (chemical composition and mechanical properties)
✅ Full material identification records linking each forging to the finished flange
✅ Heat numbers clearly stamped on every piece
This allowed the client to verify that all flanges originated from certified duplex stainless stock, compliant with ASTM A182 F51 requirements.
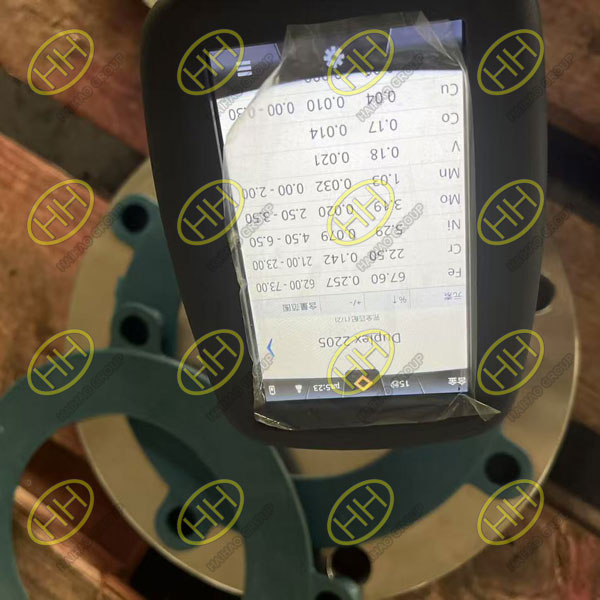
ASME B16.5 A182 UNS S31803 F51 flange chemical composition testing
Manufacturing and Heat Treatment
After rough machining, all flanges underwent solution annealing at controlled temperatures to optimize microstructure and ensure the required balance of ferrite and austenite.
We performed controlled cooling to prevent distortion and maintain dimensional accuracy, particularly critical for the smaller-diameter weld neck flanges.
Mechanical and Microstructural Testing
Before final machining and shipment, the following tests were carried out:
- Tensile Test: Confirmed yield and tensile strength within standard limits.
- Charpy Impact Test: Verified toughness at subzero temperatures per customer specification.
- Hardness Test: Ensured the hardness range complied with the project’s technical requirements.
- Metallographic Examination: Evaluated ferrite/austenite phase balance and checked for any detrimental precipitates.
Each test was documented with detailed reports included in the final quality dossier.
Visual and Dimensional Inspection
Every flange underwent a complete visual inspection to ensure there was:
- No corrosion on machined surfaces
- No scratches, dents, or deformation
- Clean, uniform raised face finish
Dimensional checks confirmed tolerances per ASME B16.5, including bolt hole spacing, flange thickness, and hub dimensions.
Packaging and Marking
To protect the flanges during transit, all sealing surfaces were covered with durable plastic caps, and each piece was securely packed in treated wooden crates with clear labels indicating:
- Nominal Size
- Pressure Class
- Material Grade (A182 F51)
- Heat Number
- Purchase Order Reference
Addressing Customer Concerns
From experience, I know European customers often have these concerns:
- How do I know the duplex microstructure is correct?
- Can you guarantee no hidden defects?
- Will documentation be complete and traceable?
By combining meticulous production control, independent mechanical tests, and full material traceability, we addressed these issues transparently.
Frequently Asked Questions (FAQ)
Q: What makes A182 F51 duplex stainless steel suitable for corrosive service?
A: F51 offers a dual-phase microstructure combining high strength with excellent resistance to pitting, crevice corrosion, and chloride stress corrosion cracking. It’s a preferred material for environments like offshore platforms and chemical processing.
Q: Can you provide impact test results?
A: Yes. For this project, we performed Charpy V-notch impact tests at -46 °C and supplied complete reports with the shipment.
Q: How do you protect flange faces during shipping?
A: All sealing surfaces are coated in rust preventive oil and protected by heavy-duty plastic caps to prevent damage in transit.
Q: Do you offer 3.1 or 3.2 certification?
A: We routinely provide EN10204 3.1 certificates. If third-party 3.2 certification is required, we can coordinate with an approved inspector (e.g., Lloyd’s, BV, TUV).
This project demonstrates how Haihao Group combines rigorous production standards, traceability, and customer-focused service to deliver high-quality flanges on schedule. Whether you need standard ASME B16.5 flanges or special materials for demanding environments, our team is ready to help you specify and produce the right solution.
For technical questions or a quotation, feel free to contact us directly. Email:sales@haihaogroup.com